5 Industrial Manufacturing Trends Impacting Your Operations
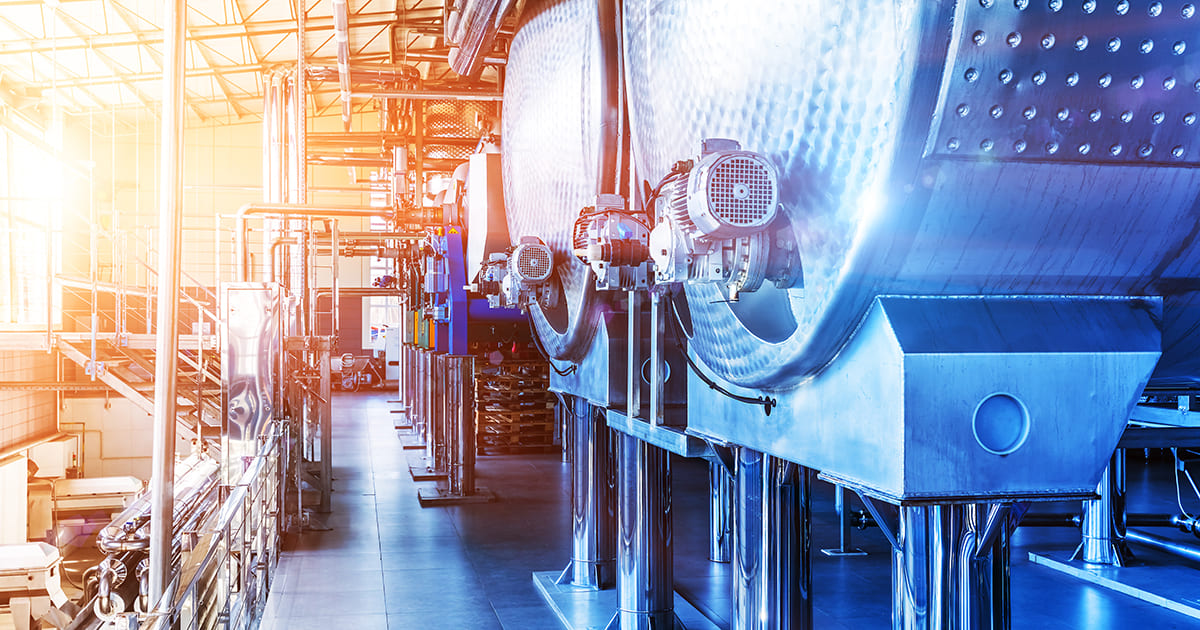
Discover five manufacturing trends that are making an impact in the post-pandemic landscape.
The manufacturing industry is constantly evolving, with significant advancements made over the last several years, particularly with Industry 4.0 technology. At Godfrey, we've kept up with the key trends in manufacturing to ensure the marketing programs we develop align with the challenges and roadmaps of target audiences. Manufacturing audiences will always be looking for solutions that improve productivity, reduce costs and ensure safety. Beyond that, the trends outlined below now challenge manufacturers to evolve their operations and marketers to align their programs to demonstrate their contribution and value in a drastically changing landscape.
As we conduct ongoing research and talk with our clients, partners and industry colleagues, several key themes have emerged:
1. Investment in Digital Transformation
No matter what we call it — digital or industrial transformation, the factory of the future — for years the concept, for some, seemed more theoretical than real. Some companies moved forward, leveraging digitalization to raise efficiency, lower costs and reduce downtime. Their efforts ran the gamut from installing sensors on machines to adopting enterprise-level systems to optimize multiple sites.
The pandemic changed the trajectory of digital transformation. As manufacturers struggled with changes that happened virtually overnight, early adopters had an advantage. With more visibility and insights into their operations, these companies could pivot more quickly in the face of a macro event impacting not only them — but also their competition.
During our Q&A with Bob Vavra, senior content director of Machine Design and Hydraulics & Pneumatics, he noted that even after COVID-19 gaps remain in the widespread adoption of smart factory solutions. He stated:
“Some of [the adoption gap] is budget-driven, some of it is talent-driven and some is a reluctance to change. Regardless, other countries and economies are embracing change and adopting digital manufacturing.”
Vavra continued to state that digital transformation is an economic imperative — one that ultimately helps save jobs and provides a competitive advantage in an increasingly global manufacturing landscape.
As manufacturers look to integrate digital transformation into their operations, it will be even more important to take a strategic, scalable and holistic approach. Starting small, getting some achievable results in key areas and then scaling up will prove beneficial, instead of trying to tackle too much and dragging out the process before any results are achieved.
2. Importance of Operational Resilience & Agility
The pandemic underscored the need for manufacturers to ensure they can continue operations even during crises or unexpected challenges. Especially during the early months of COVID-19, workers couldn’t be physically onsite and production stopped. Even though manufacturing has since resumed, companies continue to work through backlogs that prevent them from operating at maximum efficiency and providing the best-possible service to customers.
Along with the need for better resiliency, manufacturers are also faced with increasing customer expectations around individualized or small-lot production. They are being challenged to offer the flexibility to provide production runs numbering in the tens of thousands to those with a lot size of one.
Smart automation solutions can help manufacturers increase resiliency and agility. Whether adding more sensors and robots or leveraging machine learning and artificial intelligence, these tools can serve as a safety net that allows the plant to keep running, as well as support fast, seamless and profitable changeovers to meet the evolving needs of customers or the market.
As we move into the post-pandemic landscape, manufacturers will likely look to emerging technologies, like 5G communication, to employ more smart automation and, beyond that, lights-out manufacturing that enables production to continue without onsite staff.
3. Focus on the Team: Skills & Safety
Conversations around smart automation often lead to questions about the technology’s potential to impact the workforce. But that shift toward intelligent factory technologies is more about an evolution that shifts job skills requirements rather than replaces them.
As automation takes on more high-volume, repetitive or dangerous tasks, skilled labor is needed to interact collaboratively with smart machines. It’s critical for manufacturers to train up their workforce for these new digitally demanding jobs with initiatives like retraining, vocational or STEM programs.
Safety has always been a top priority for manufacturers. As technology evolves, safety protocols and training will need to evolve with it. For example, increased automation, particularly the use of robots, can require enhanced safety measures. John Sprovieri, editor-in-chief of ASSEMBLY magazine, told us during our recent Q&A:
“A standard industrial robot is dumb. It only goes where it’s programmed to go, and if someone gets in its way, that person could get seriously hurt … The increasing popularity of cobots represents both a benefit and a risk for manufacturers. Yes, cobots are designed to work safely next to people on assembly lines without traditional safety guarding. But that doesn’t mean every application is inherently safe. Every application needs to be assessed for risks.”
4. Shift Toward Local Production
There’s no doubt that the pandemic disrupted supply chains; however, the disruptions can provide manufacturers with opportunity. John Sprovieri said during our Q&A:
“If there’s a silver lining to the pandemic, it might be that it encourages U.S. manufacturers to consider reshoring production — to make more goods domestically and import less. Last year’s shortages of personal protective equipment, ventilators, pharmaceutical ingredients and other medical products opened a lot of eyes in board rooms and in Washington.”
Combined with other factors, like manufacturers’ need for better operational agility and tariffs, companies are now reevaluating how they source their products. Rather than importing raw materials, manufacturers are looking toward building smaller, more localized ecosystems. During our Q&A with Design World, VP and Editorial Director Paul Heney stated that the challenge facing industrial manufacturers now is to find a sweet spot for reshoring production. He said:
“[I]nstead of having one manufacturing facility in China, a company would have 4-6 smaller ones in different regions of the world, maybe Wisconsin, Brazil, South Korea, the Czech Republic and India. This approach seems to make more sense to me, but it wouldn’t surprise me if the pendulum swung back in another decade or two."
The shift toward a more localized ecosystem may also lead manufacturers to locate their operations closer to their customers. This positions companies to provide more agile service to customers, as well as decrease time to market, reduce working capital and build resiliency.
5. Growing Need for Sustainable Manufacturing
From customers and investors to leadership and employees, manufacturers’ stakeholders have increased their focus on sustainability. This shift is leading to the creation of values-based initiatives that not only make sure their manufacturing processes reduce waste — but also that the solutions they provide help customers’ meet their own sustainability goals.
Regulatory bodies across the globe play a role as well. Whether it’s a local water use ordinance or a national ban on a specific chemical, manufacturers must also ensure they stay compliant with constantly evolving regulations.
Even as demands for sustainable practices increase, a core challenge remains for manufacturers. In our Q&A, Bob Vavra commented:
“Sustainability has to be profitable, or at least cost-neutral, for manufacturers to fully embrace it. I think viewing energy as a cost that can be managed rather than a bill that needs to be paid goes a long way to greater understanding of the true costs and benefits of sustainability.”
The key to success in sustainability is rooted in a values-based strategy that uses operationally based initiatives. In addition, manufacturing trends we’ve already looked at, like automation and IoT technology, can help manufacturers implement sustainable processes that improve efficiency, reduce energy usage, lower carbon footprint and leverage renewable resources.
The only thing constant is change.
From emerging technologies to macro events, industrial manufacturing trends will continue to evolve. Understanding how these trends impact manufacturing audiences can help marketers ensure they are providing the education, support and relevancy needed to stand out in the competitive landscape.
Sign Up for our Newsletter - Get agency updates, industry trends and valuable resources delivered directly to you.
Alison Fetterman - Vice President, Strategy & Analytics
Alison leads the strategy and analytics teams, focused on driving insightful and innovative ways to connect with clients’ audiences and clearly show a strong ROI for Godfrey’s B2B marketing programs.